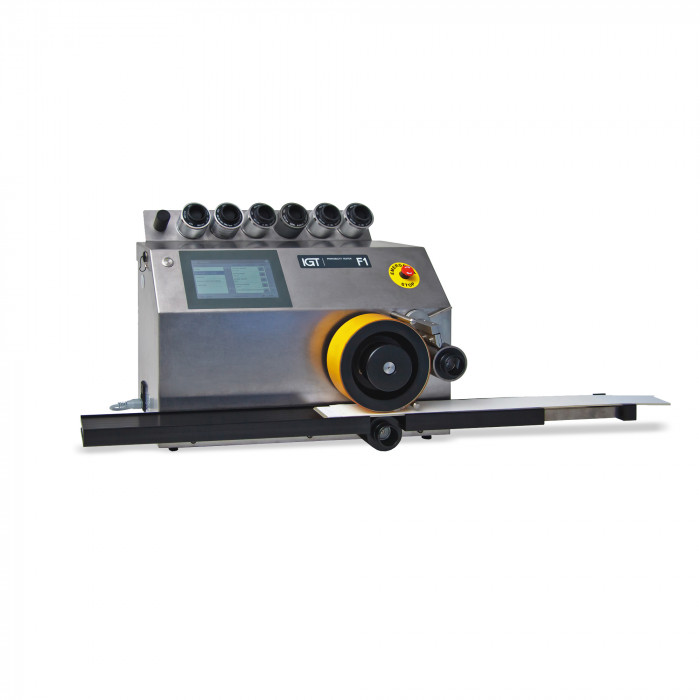
F1
F1: printability tester for flexo inks. Can also be used for gravure prints.
The F1 is universal flexo tester for use with solvent based inks, UV inks and water inks on a range of substrates. The F1 is available with facilities for printing on corrugated board and for gravure printing. lso available as the F1-UV with integrated UV dryer.
•High reproducibility
•Simple to operate
•Consistent results
Worldwide the best printability tester for solvent based, UV curing and water based flexo inks.
Includes gravure mode!
NEW: Now pre-inking of the anilox roller for even better results!
Makes colour strips with flexo or gravure inks which can be used for many purposes.
Specially designed for computerized colour measuring and colour matching systems.
Saves costs because colour matching tests on the printing presses are no longer necessary.
APPLICATIONS
The F1 printability tester produces colour strips suitable for many purposes, such as:
•Measuring colour with colour measuring systems or spectrophotometers.
•Use in colour matching systems, visual appraisal, density measurements, including establishing colour and density tolerances and determination of coverage, wear resistance, scratch resistance, flexibility, adhesion and gloss, ink transfer, light fastness and resistance to chemicals
• Testing print quality.
The F1 tester prints all sorts of coated and uncoated materials:
paper, board, plastic film, cellophane, laminate, labels, textiles etc.
The F1 tester is used in the following industries:
•printing ink, paper and board, printing
•plastics, packaging and labelling
•resins, lacquers and coatings
•raw materials
PROPERTIES
The principal properties of the F1 are:
•Simple to operate and easily movable; very reliable and of sturdy construction for intensive use over a long period; easy and quick to clean
•Extensive processing possibilities for various substrates and inks; substrate, ink, engraved roller (available in many sorts) and printing form simple and quick to change
•Makes a two anilox revolution print
•Can ink the photopolymer up to twenty times before making the print
•Excellent reproducibility, high degree of simulation of actual practice Electronic printing force and speed control
OPERATION
The F1 tester consists of a combination of inking section with engraved anilox roller and doctor blade and a printing section with printing form (photopolymer) and an impression cylinder. The substrate is attached to a carrier and placed on the substrate guide, between the printing form and the impression cylinder. When the F1 is activated, the anilox disc and the substrate come into contact with the printing form and the doctor blade contacts the anilox.
With the aid of a pipette, a few drops of ink are applied to the nip between the doctor blade and the anilox. During the print the ink is wiped off and transferred from the anilox disc to the printing form and from the printing form to the substrate. Doctor blade, anilox disc and impression cylinder are then lifted automatically. In the multiple revolution mode the substrate is brought in contact with the printing form after the preset number of revolutions are made.
The substrate is removed for appraisal. The anilox disc, doctor blade and printing form are cleaned. In flexography the printing quality depends very much upon the printing speed, which is therefore adjustable from 0.2 to 1.5 m/s.
A two revolution print is made because this fills the engraved disc as well as possible with ink. The second part of the print is most suitable for evaluation. Between impression cylinder and printing form there is about 4 mm space, so that thick materials, like corrugated board, also can be printed.
The force between the anilox and the printing form and between the printing form and the substrate can be set independently between 10 and 500 N.
In case of the gravure mode the print is made on the substrate which is mounted directly on printing form cylinder.
Driven anilox roller, to ink the anilox roller independently. The F1 consist of a combined inking unit with doctor blade, anilox roller and a printing unit with printing form and impression cylinder. Especially developed to print strips with flexographic ink. Gravure mode for gravure ink.
•Electronic printing force and speed setting and control
•Flexo or gravure mode selection
•Printing speed: 0.2 -1.5 m/s
•Printing force: 10 – 500 N
•Impression cylinder and engraved disc are automatically brought under pressure, printed and lifted
•Doctor blade is automatically placed against engraved disc and lifted
•Maximum substrate thickness 4 mm
•Printing width on substrate: 40 mm
•Printing length on substrate: 200 mm (2nd print)
•Engraved disc is inked twice
•Photopolymer cylinder can be inked up to 20 revolutions
Engraved discs
Several versions are available for the application of different quantities of ink. Special engraved discs can be made on specification.
A full range of gravure printing forms is available.
Flexo: copper, chromium plated or ceramic, laser engraved including banded versions
Gravure: copper, chromium plated different standard layouts including Heliotest, or on customer specification
Screen ruling: 40 – 140 l/cm (100-360 l/inch)
Volumes: 4 – 26 ml/m2
Doctor blade
•Doctor blade angle: 60o, trailing
•Doctor blade pressure: 6 – 7 N
Printing form and printing cylinder
The F1 tester has several printing forms: solid and screened, in rubber and photopolymer. Customers’ printing forms also can be used. The printing form is attached to the printing form cylinder with cliché (foam) tape.
Substrate carrier
The substrate carrier consists of a strip of plastic, covered with foam and hard polyester.
General
•Complies with EC directives
•Modern styling
•Reliable
•Low initial cost
•Suitable for many substrates and inks
•Easily movable
•Detailed instructions for use
Weight : 35 kg
Size: 300 x 650 x 400 mm
Electrical rating:115/230 V-50/60 Hz
Weight: | 35kg |
Dimensions(L x W x H): | 0cm x 0cm x 0cm |
Model: | 432.000.000 |
Main application: | Print substrate with flexo or gravure inks for colour measurement colour-matching visual appraisal of print quality density measurements and measurement of properties such as wear resistance scratch resistance fastnesses mottle etc. |
Conformance with standards/W-leaflet: | ISO 2834-2 / ISO 2836 / ISO 2846-3 / ISO 2846-5 |
Water bath and temperature: | — |
Speed range and modes: | Constant: 0.2 – 1.5 m/s |
Forces: | Anilox force: 10 |
Substrate requirements: | Flexible and rigid substrates |
Interval time and number: | — |
Printing shafts type and options: | 1 shaft |
Shaft positioning: | Automatically |
Lifting system: | Automatically |
Print length and width: | 2x 200×40 mm_ |
Printing discs: | Chromium plated in copper engraved ceramic laser engraved anilox discs various line rulings and volumes |
Sector positioning: | Automatically |
Sector type and options: | Exchangeable 154 |
Doctoring system: | Doctor blade, 60 |
Dispensing system: | — |
Pre-programmed tests: | Several test methods and conditions are preset. Can easily be changed by the user. |
Analysis options: | Off-line with Print Target |
Interfaces: | USB |
Software updates: | USB |
Data export options: | USB, CSV file |
Additional items: | 496.000.075 UV Dryer Aktiprint mini 12-1 1 lamp 500 W 496.000.275 UV Dryer Aktiprint mini 12-1 2 lamps 1000 W 495 Lightbooth with 4 lightsources (A UV D65 F10) 555.000.060 IGT Glossmeter G60 (60 |
Accessories: | 431.000.439 Gravure set |
Inks or liquids: | Flexo and gravure inks |
Inking speeds: | 0.2 |
Inking programs: | Number of doctoring revolutions 0 – 9, Number of revolutions before print 0 – 20 |
Top rollers: | — |
Maintenance: | Yearly. The annual maintenance and calibration of the tester can be carried out by IGT Testing Systems or companies authorized by IGT Testing Systems. Information can be obtained from your supplier or the local agent. |
Compatible instruments: | 421.000.100 F1 Basic High Force Range421.000.200 F1 Basic Low Force Range |
Measurement range: | — |
Light source/ power/angle: | — |
Volume: | — |
Shelf life: | — |
Use life: | — |
Description of property: | — |
Cleaning: | Cleaning mode for anilox and printing forme. |
Power Supply Requirements: | 115/230V/2.5AT/50-60 Hz/250VA |
Guarantee: | Standard one year |
Space requirements: | 0.7 m_ |
Standard delivery time: | 6-8 weeks |